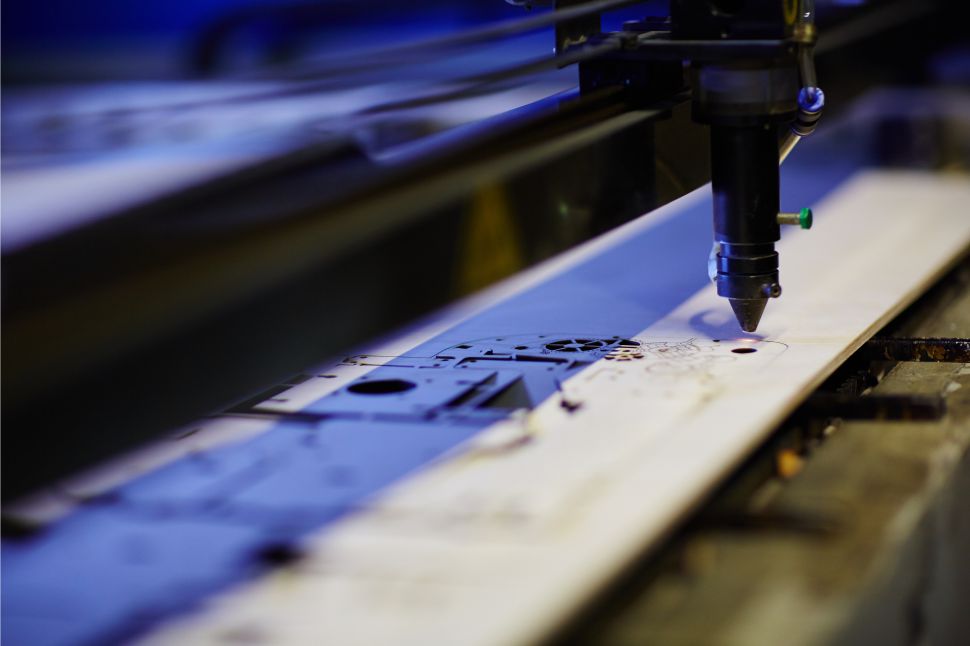
Our product design and engineering services includes 3D CAD modelling, reverse engineering, product detailing for plastics and metals, design for manufacturing studies (DFM/DFMEA), product re-engineering, value engineering to study alternate manufacturing methods, cost optimization. Furthermore, the team at GAK Enterprises Limited has a great deal of collective experience in several domains, which enables us to provide consulting services in almost any field. We have consulted on a wide range of projects to both Governmental and Non-Governmental organizations. Our vision is to help the start-ups and organizations with limited resources to build revolutionary products with the help of our experience and resources fostering the growth of both organizations.
- Seating Systems
- Automotive interiors/ exteriors
- Automotive BIW
- Medical products
- Machine Design
- Static, Dynamic & Fatigue Testing
- Multi-physics
- Computational Fluid Dynamics
- Value Engineering
- Vehicle E/E Engineering
- E/E Systems Engineering
- E/E Verification Validation
- R & D in Electrical and Electronics
- Robotics
- Indigenous Products
- Firmware & Software
- Strong Design capability for practical solutions and designed for manufacturability.
- Simultaneous engineered BIW design.
- Lightweight BIW solutions.
- Design capabilities – Wiring harnesses, connectors, moulded plastic components, injection moulding tools, rear vision systems and complete module designing and strong benchmarking experience.
- Safer BIW structures to meet the requirements.
- Instrument Panel
- Centre Console
- Door Trims (Soft & Hard skin)
- Garnish Trims
- Luggage compartment
- Impact beam
- Seating
- Bumper & Front end module
- Body side Cladding & Garnish
- Rocker Moulding
- Roof Rail System
- Exterior Grill
- Head light interface
- Benchmarking
- Tolerance Stack-up Analysis
- Flush-Gap study
- Homologation & Localization Support
- Manufacturing & Assembly Feasibility
- Package development
- Static & Dynamic clearance studies
- Interface development
- Sub-system interface development
- DFA evaluation
- Component & system tolerance study
- Reverse Engineering
- Support styling & studio requirements
- Support panel for feasibility
- Assembly fitment/Removal study
- Static/Dynamic clearance
- Forming feasibility material
- Material selection based on the joint & tolerance
- Component breakdown
- Incorporate styling lines
- Develop master sections
- Accommodate aggregate
- Positioning to ensure function
- Ergonomics study
- Process development based on section requirement
- Support styling & studio requirements
- Support panel for feasibility
- Assembly fitment/Removal study
- Static/Dynamic clearance